
The production structure of the Milazzo Refinery, originally based on a simple cycle, was expanded using major investments planned in the second half of the 1980s and aimed to:
- increase the conversion capacity, i.e. the ability to transform crude oil into finished products, compared to oil distillation alone
- maintain the production of the entire range of finished products in compliance with increasingly stringent legal limits.
Since the 1990s, constant development and technological upgrading interventions have been implemented on the plants to obtain better results in terms of production, thanks to maximum efficiency and improved performance. Plants that operate efficiently make it possible to avoid production interruptions and other inefficiencies, reducing safety risks
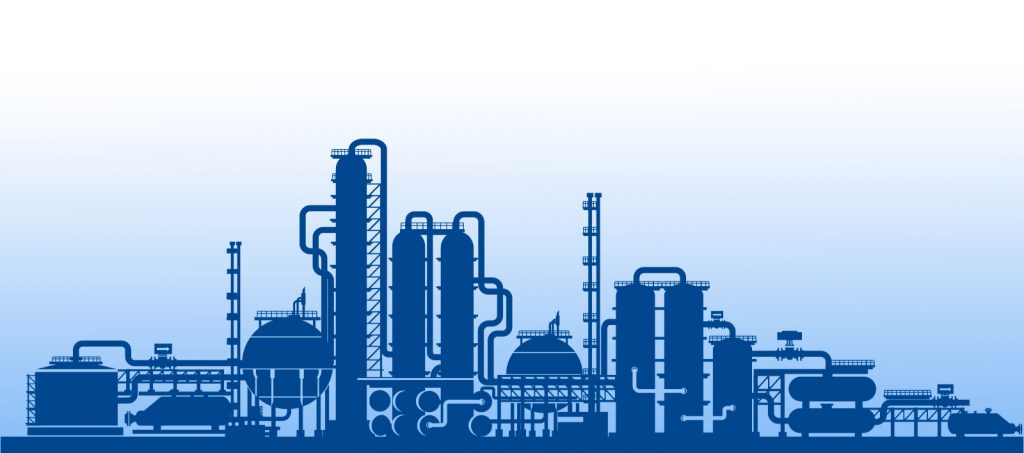